Custom Rubber Molding
From Design To Delivery
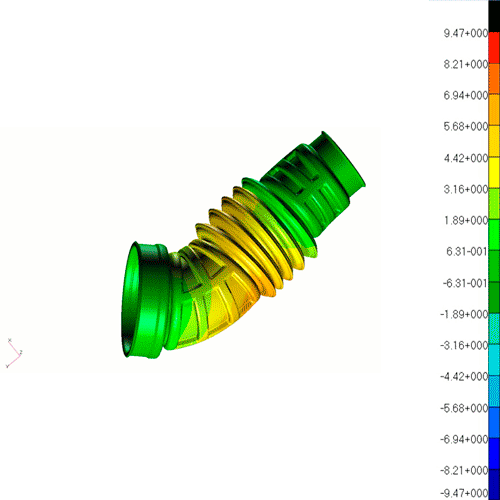
Can’t find the Rubber part you need? Let's DO It!
Whether you know your specs or you need help designing just the right piece, we’ll make the part that will work for you.
Bonding techniques are available today. The process — from initial concept to finished product — is often quick and low cost.
Tailored Rubber Solutions
Creating rubber parts that are perfectly aligned with the unique demands of your industry.
Innovative Design Assistance
Providing expert assistance in product and mold design for successful market outcomes.
Diverse Material Options
Offering a variety of rubber materials tailored to meet your project's specific needs.
Need a unique rubber part? Let's make it happen!
Bring your vision to life with us! Contact us today and let’s embark on a journey to craft your ideal rubber part, ensuring excellence every step of the way.
Custom Rubber Manufacturing Process
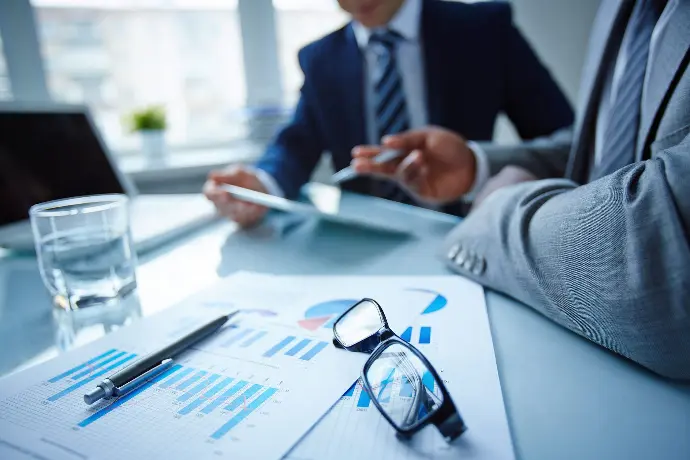
Step 1: Consultation and Requirement Analysis
The process begins with a thorough consultation where we engage with you to understand your specific needs. During this phase, we focus on:
- Project Scope: Defining the type of rubber part required, including dimensions, tolerances, and functional requirements.
- Material Selection: Providing recommendations for the most suitable rubber material based on your application's specific environmental factors.
- Production Volume: Determining the required quantity to choose the best molding method (compression, injection, or transfer).
- Budget and Timeline: Align your budget and timeline expectations with our production capabilities.

Step 2: Design and Engineering
Once the requirements are clearly defined, our engineering team takes over to develop a detailed design plan. This phase includes:
- CAD Modeling: Using advanced CAD software, we create 3D models of the rubber part. These models allow us to visualize the final product and make any necessary adjustments before the mold creation begins.
- Prototyping: Depending on the project, we may produce prototypes using rapid prototyping techniques. These prototypes enable you to test the fit, form, and function of the design before proceeding to full-scale production.
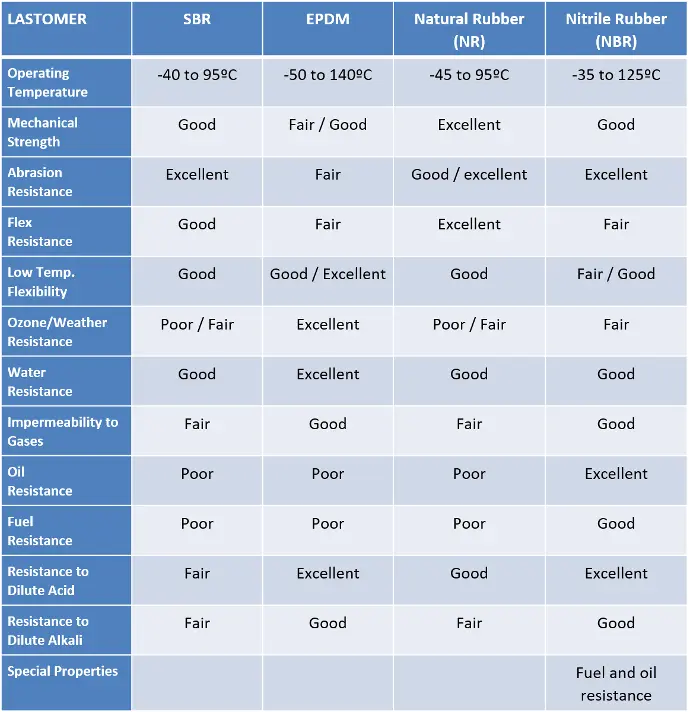
Step 3: Material Selection and Testing
Material selection is key to project success. We provide various rubber options tailored to specific needs.
- Material Analysis: Evaluating the performance characteristics of different materials, including their resistance to heat, chemicals, and wear.
- Sample Testing: In some cases, we may produce small batches of test samples to ensure the chosen material meets the required performance criteria.
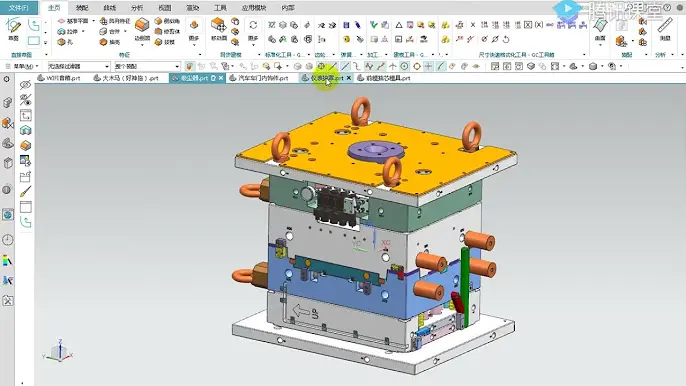
Step 4: Mold Design and Fabrication
Finalized design and selected material, now onto mold creation:
- Mold Design: Our tooling engineers create custom molds based on CAD models for precise part production.
- Mold Fabrication: We use high-quality steel to fabricate the molds, ensuring durability and consistent performance throughout the production run.
- Testing and Validation: We test the mold with a trial run to ensure accurate and consistent part production before full-scale manufacturing.
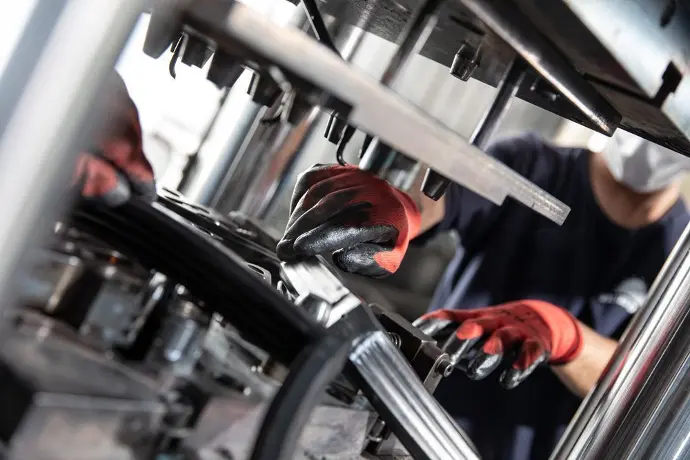
Step 5:
Production
After validating the mold, we move on to the production phase and choose the appropriate molding process based on project requirements.
- Compression Molding: Ideal for producing large, durable parts with excellent material properties. The rubber material is placed into the mold cavity, and pressure is applied to shape it into the desired form.
- Injection Molding: Suitable for high-volume production of intricate parts with tight tolerances. Rubber is heated and injected into the mold under high pressure, ensuring uniformity and precision.
- Transfer Molding: A versatile process that involves pre-heating the rubber before it is transferred into the mold cavity. This method is often used for parts with complex geometries or when a higher degree of control over material flow is required.
During production, we continuously monitor the process to ensure that every part meets our quality standards.
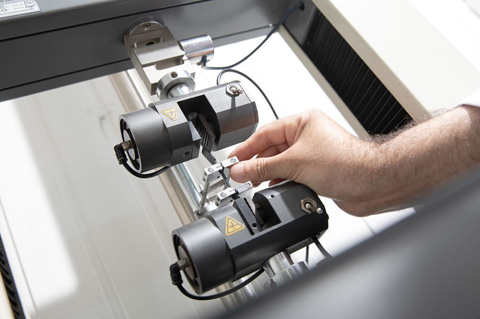
Step 6:
Quality Control and Inspection
Quality is at the core of our operations, and we implement rigorous quality control measures throughout the production process:
- In-Process Inspection: Our technicians conduct inspections at various stages of the molding process to identify and correct any issues promptly.
- Dimensional Verification: Each part is measured to ensure it meets the specified dimensions and tolerances.
- Material Testing: We perform tests to verify the material’s properties, such as hardness, tensile strength, and elasticity.
- Final Inspection: Before packaging, every part undergoes a final inspection to confirm that it meets all specifications and quality standards.
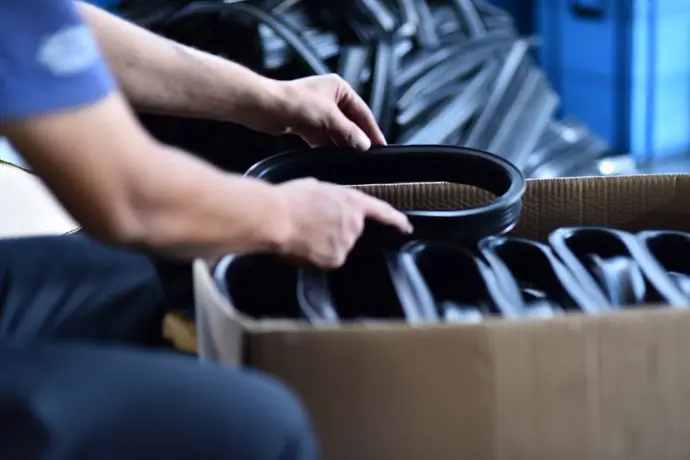
Step 7:
Packaging and Delivery
Once the parts have passed all quality checks and any post-molding operations are completed, we carefully package them to prevent damage during transportation. We offer:
- Custom Packaging: Tailored to meet the specific needs of your products, ensuring they arrive in perfect condition.
- Timely Delivery: We coordinate with reliable logistics partners to ensure that your order is delivered on time, whether it’s a small prototype batch or a large production run.
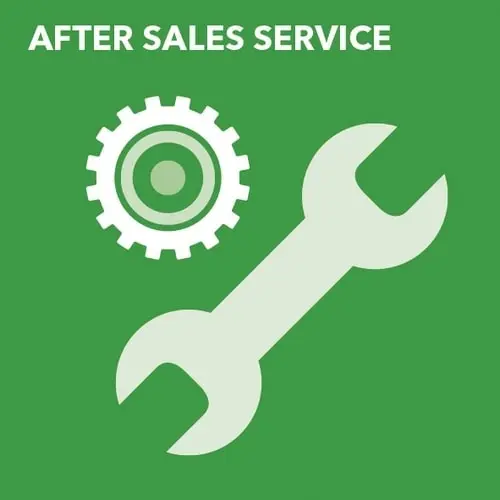
Step 8:
Continuous Support and After-Sales Service
Our dedication to customer satisfaction goes beyond delivery. We offer:
- Technical Support: Ongoing assistance with any questions or issues you may encounter with your molded parts.
- Future Production Runs: If you need additional parts or adjustments, we maintain your mold and production records for quick turnaround on future orders.
Frequently Asked Questions
Custom rubber molding is a specialized manufacturing process where rubber components are designed and produced according to specific requirements provided by the client. Unlike standard rubber molding, which uses pre-designed molds for generic parts, custom rubber molding involves creating unique molds tailored to the exact dimensions, shapes, and material properties required by the customer’s application. This ensures that the final product meets precise functional and performance criteria.
CRYSTAL Rubber Factory offers a wide range of rubber materials to suit various applications, including:
- EPDM (Ethylene Propylene Diene Monomer): Known for excellent weather and ozone resistance, ideal for outdoor and automotive applications.
- Silicone: Offers high-temperature resistance and is often used in medical, food-grade, and automotive applications.
- Neoprene: Durable and resistant to oils, chemicals, and weathering, making it suitable for industrial and automotive uses.
- Nitrile (Buna-N): Excellent oil and fuel resistance, commonly used in automotive and aerospace industries.
- Natural Rubber: Provides superior elasticity and tensile strength, ideal for industrial applications that require high durability.
We also offer other specialty materials depending on your project’s specific needs.
The lead time for custom rubber molding projects at CRYSTAL Rubber Factory can vary depending on the complexity of the design, the type of material used, and the production volume required. Generally, the lead time includes:
- Design and Prototyping: 2-4 weeks, depending on revisions and approvals.
- Mold Fabrication: 4-6 weeks, depending on the complexity of the mold.
- Production and Delivery: 2-3 weeks after mold approval, though high-volume orders may take longer.
We strive to work within your timelines and can expedite the process if necessary.
Yes, CRYSTAL Rubber Factory is equipped to handle both low and high-volume production runs. Our advanced molding facilities, coupled with automated processes, allow us to maintain consistent quality across large orders while ensuring timely delivery. Whether you need a small batch for prototyping or a large-scale production run, we have the capacity to meet your needs.
Quality is a top priority at CRYSTAL Rubber Factory. We implement rigorous quality control measures at every stage of the manufacturing process, including:
- Material Inspection: We carefully select and test raw materials to ensure they meet the required specifications.
- In-Process Monitoring: Continuous monitoring during the molding process to maintain consistency and accuracy.
- Dimensional Verification: Precision measurements of each part to ensure they meet the specified tolerances.
- Final Inspection: Comprehensive checks, including visual inspection and material testing, before packaging and delivery.
We adhere to ISO standards to guarantee that every product we deliver meets the highest quality benchmarks.
CRYSTAL Rubber Factory serves a wide range of industries, including but not limited to:
- Automotive: Custom seals, gaskets, and vibration dampeners.
- Aerospace: High-performance seals and components that can withstand extreme conditions.
- Medical: Biocompatible silicone parts for medical devices and equipment.
- Construction: Durable rubber components for building and infrastructure projects.
- Electronics: Insulating materials, gaskets, and custom enclosures for electronic devices.
- Industrial: Custom rubber parts for machinery, equipment, and heavy-duty applications.
We have the expertise to cater to the specific needs of these and other industries, ensuring that our products meet their unique requirements.
Absolutely. Our team of experienced engineers and designers is here to help you through the entire design and prototyping process. We use advanced CAD software to create detailed 3D models of your parts, allowing you to visualize and refine the design before moving to production. We also offer rapid prototyping services to create physical samples that you can test and evaluate before finalizing the design.
CRYSTAL Rubber Factory offers custom color matching services to ensure that your rubber components meet your specific aesthetic requirements. Whether you need a specific color for branding, safety, or coding purposes, we can match and produce rubber parts in the exact shade you need.
Yes, we offer a range of post-molding services to enhance the functionality and appearance of your rubber parts, including:
- Deflashing: Removing excess material for a clean finish.
- Custom Finishing: Applying surface treatments, coatings, or color matching.
- Assembly: Integrating molded parts into larger assemblies as required.
These services ensure that your parts are ready for immediate use upon delivery.
To get started with a custom rubber molding project at CRYSTAL Rubber Factory, simply contact us to discuss your needs. Our team will guide you through the initial consultation, where we will gather information about your project, such as the required material, dimensions, performance characteristics, and production volume. From there, we will assist with design, material selection, and provide a detailed quote and timeline for your project.
Haven't found your rubber match yet? Let's customize it now!
Ready to create something exceptional? Reach out today and let's start shaping your perfect rubber part, ensuring precision and satisfaction from concept to completion